I have a stepper motor with a 18 mm shaft and a 6mm keyway cut into the shaft.
I want to mount a sprocket on the motor shaft that can use a bicycle chain. The chain my bicycle sprocket will use is 1/2" pitch by 1/8" width. I believe this chain is also known as ANSI 43.
My problem is that so far I haven't been able to find a bicycle sprocket that I can mount on my 18 mm shaft. I have come up with a few alternatives, which I will describe below, but if anyone has dealt with this problem or similar I would greatly appreciate the advice.
1)
I take an ANSI 40 sprocket that does mount on my 18 mm motor shaft, and I grind down the teeth on the sprocket until they are narrow enough for the ANSI 43 chain to be slipped over.
This has the advantage of simplicity, but the sprockets are made of 1045 Carbon Steel with hardened spurs. Grinding down the teeth could end up difficult, time consuming, and if I ever want to change the sprockets on my motor to something different I'll have to grind down a new sprocket.
2)
I get a flanged shaft collar (some are sold at McMaster Carr), get an ANSI 40 machinable plate sprocket, and drill holes in the plate sprocket so that I can bolt it to the flanged shaft collar. I would also need to grind down the teeth of the ANSI 40 sprocket until the bike chain could fit on the sprocket.
Below is a picture of the flanged shaft collar.
3)
I get a flanged shaft collar, and then I try to find a bicycle socket whose holes happen to align with the flanged shaft collar's and hope it works.
Seeing as a lot of bicycle sprockets don't list things like bolt hole diameter, I'm not sure how I'd do this besides ordering stuff and hope I get lucky, or buy the flanged shaft collar, visit bike shops, and hold it up to bike sprockets.
4)
I buy a fixed gear hub, take out the axle and all the internal components, slide the hub onto my motor shaft, and then find a way to affix it to my motor shaft. Probably by drilling holes into the hub and installing set screws. Then I just install a normal fixed gear on the hub.
The main problem here is that my motor shaft has an 18 mm diameter, which is significantly wider than most bike axles. Which would mean I'd need to attach a smaller axle to the motor shaft, and then mount the hub on the smaller axle.
These are the main ideas I've come up with so far. Does anyone have any suggestions, or their own ideas? If anyone has any kind of experience with this sort of work, I'd be very interested to hear their advice. Or if you foresee any problems with these methods.
If anything needs to be clarified, just ask. Thanks in advance for any feedback you can give.
I want to mount a sprocket on the motor shaft that can use a bicycle chain. The chain my bicycle sprocket will use is 1/2" pitch by 1/8" width. I believe this chain is also known as ANSI 43.
My problem is that so far I haven't been able to find a bicycle sprocket that I can mount on my 18 mm shaft. I have come up with a few alternatives, which I will describe below, but if anyone has dealt with this problem or similar I would greatly appreciate the advice.
1)
I take an ANSI 40 sprocket that does mount on my 18 mm motor shaft, and I grind down the teeth on the sprocket until they are narrow enough for the ANSI 43 chain to be slipped over.
This has the advantage of simplicity, but the sprockets are made of 1045 Carbon Steel with hardened spurs. Grinding down the teeth could end up difficult, time consuming, and if I ever want to change the sprockets on my motor to something different I'll have to grind down a new sprocket.
2)
I get a flanged shaft collar (some are sold at McMaster Carr), get an ANSI 40 machinable plate sprocket, and drill holes in the plate sprocket so that I can bolt it to the flanged shaft collar. I would also need to grind down the teeth of the ANSI 40 sprocket until the bike chain could fit on the sprocket.
Below is a picture of the flanged shaft collar.
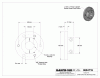
3)
I get a flanged shaft collar, and then I try to find a bicycle socket whose holes happen to align with the flanged shaft collar's and hope it works.
Seeing as a lot of bicycle sprockets don't list things like bolt hole diameter, I'm not sure how I'd do this besides ordering stuff and hope I get lucky, or buy the flanged shaft collar, visit bike shops, and hold it up to bike sprockets.
4)
I buy a fixed gear hub, take out the axle and all the internal components, slide the hub onto my motor shaft, and then find a way to affix it to my motor shaft. Probably by drilling holes into the hub and installing set screws. Then I just install a normal fixed gear on the hub.
The main problem here is that my motor shaft has an 18 mm diameter, which is significantly wider than most bike axles. Which would mean I'd need to attach a smaller axle to the motor shaft, and then mount the hub on the smaller axle.
These are the main ideas I've come up with so far. Does anyone have any suggestions, or their own ideas? If anyone has any kind of experience with this sort of work, I'd be very interested to hear their advice. Or if you foresee any problems with these methods.
If anything needs to be clarified, just ask. Thanks in advance for any feedback you can give.
Last edited: