Not much to say, I've made some changes to the original plans, substituting the o&r for an old homelite chainsaw, and also I've made the height of the frame 11 inches. I used 3/4 inch 16 gauge tubing to make these frame parts. I got the wheels and tires for 5$ each on clearance at northern tool, and not pictured is all of the sprockets I've acquired as.well. I'll let the few pics I've got do the speaking from.here, and I'm building this as a school welding project.
What it might end up looking like
Ccd
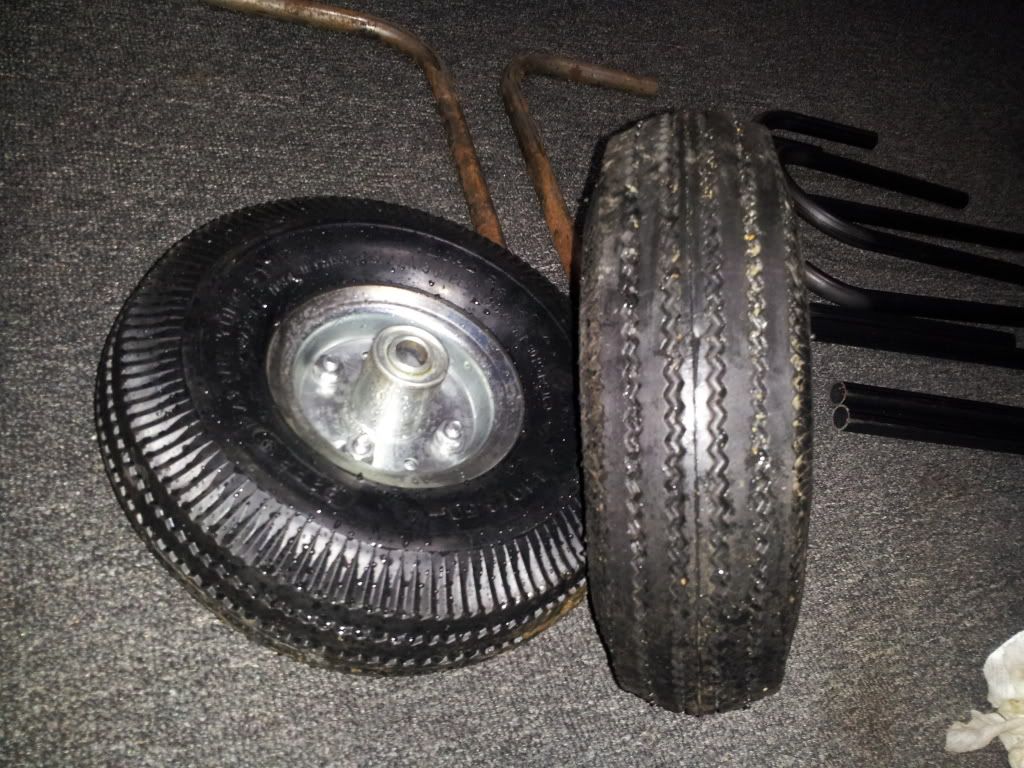
What it might end up looking like
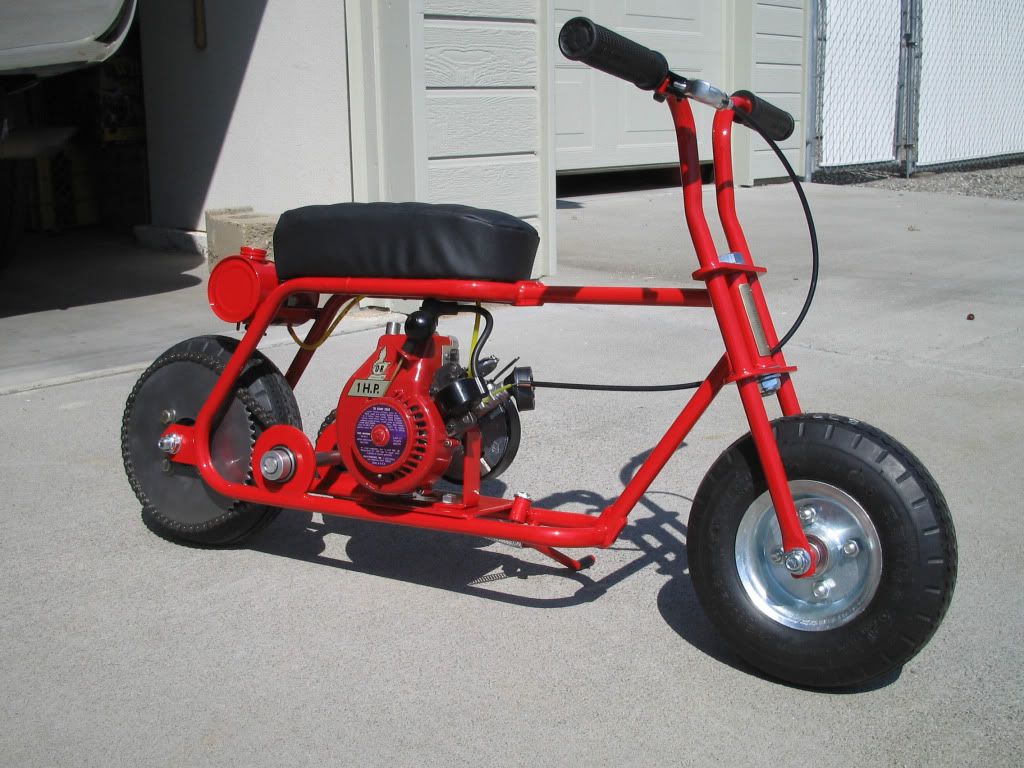
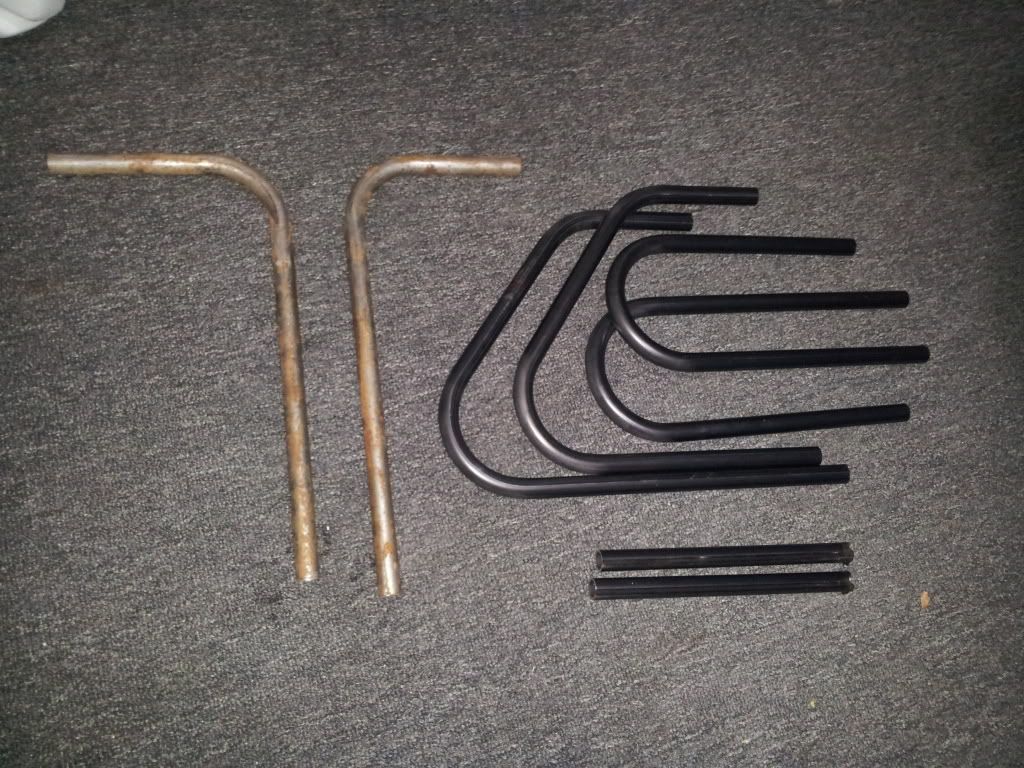
Ccd