So as I trudge on searching and scraping for info on powells I found a guy to finally give me the specs on the shifter pad that’s mounted on the top of a c model frame…..I will attempt to make one…..
Using a slab from a roll of industrial belt from the plant….
we got this templet….its supposed to be 9/16” thick…,I’m going 3/4 because my belt is a tad thinner I’m putting a piece of 1/16” mild steel cut to pattern….
Then cut out another piece of rubber and bind it together with industrial adhesive….we’ll see if it works…they say they wear out we’re trying to stop thst….this is what one should resemble….
I’ll post finished product in a day or two….
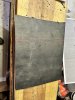
Using a slab from a roll of industrial belt from the plant….
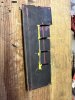
we got this templet….its supposed to be 9/16” thick…,I’m going 3/4 because my belt is a tad thinner I’m putting a piece of 1/16” mild steel cut to pattern….
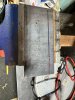
Then cut out another piece of rubber and bind it together with industrial adhesive….we’ll see if it works…they say they wear out we’re trying to stop thst….this is what one should resemble….
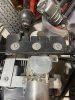
I’ll post finished product in a day or two….
Last edited: