The following is a reprint of a post I made on both CNCzone.com and plasmaspider.com on 19 May 2014, but thought would be equally as valuable here. Hopefully it will serve as an educational tool for at least one person out there and save them from making the same mistake I did upon entering the world of CNC plasma fabrication.
13.6 miles. That’s how far I made it down the road after picking up my brand new 4x2 Burntables CNC table. I stopped to check my trailer to make sure my cargo was properly secured and was greeted by a handful of washers, nuts, bolts and bearings laying on my trailer. I promptly snapped the following picture and emailed it to Matt Kool, the salesman I dealt with at BurnTables. His reply: “Yes, a little tighter would have been preferred.”
It’s also worth noting that I removed (by hand) other hand-tight bolts and bearings at this point so as not to lose them on the rest of the way home. Makes me wonder how such a table was tested at the factory prior to shipment/pick-up… This should have been my first red flag about the quality issues I was soon to experience with BurnTables, but those were actually raised before my purchase as several other victims of BurnTables’ sales pitch had advised me to stay far far away from this product. Failing to heed their advice, I did indeed end up taking the leap and making this purchase, which I have regretted literally since day one.
It took a couple of weeks before I was able to complete the installation of the table in my shop and actually begin trying to use it. Immediately, I was greeted with the following examples of the table’s work:
I was assured, however, that the problems I was experiencing were due to the fact that I was using a Hypertherm PowerMax 45 plasma cutter and their table’s Torch Height Control had a very small window of compatibility with this particular plasma cutter, but to keep adjusting their THC knob and eventually I would find the “sweet spot.” I finally was indeed able to eventually make what I thought were acceptable cuts. As it turns out, I would have been happy with ANY completed cut, regardless of quality. Starve a man long enough and he’ll eat anything, right? This small time frame of “success” was short lived, however, as simply changing the consumables of my machine torch threw the machine so far out of whack that I once again could not even come close to completing a cut, often not even moving the torch once the initial pierce was made. More knob turning. More knob turning. Calls to “tech support.” Instructions to keep turning the knob. Literally hours of knob turning. It was at this point I realized I was fighting an uphill battle. If this was standard operating procedure for recalibrating the machine after a simple consumables change, I was dealing with an unacceptable piece of equipment that at its best, wasn’t good enough. This is when I first asked for a refund for the table, a request which was ignored, and instead was offered the chance to send in my computer, controller, and plasma cutter for inspection and testing. Instead I packed it all up and drove it back to BurnTables myself. After a few hours onsite with Kyle Riggens (owner) and CJ Ortiz (tech support), they swapped not only my control box (because of an unknown internal issue), but also my Hypertherm unit for brand new ones. Before my experience with BurnTables, my Hypertherm was a perfectly functioning cutting unit. After they made their requisite internal modification to my torch, however, it threw an internal breaker multiple times every time I turned it on. As soon as Kyle was made aware of this, he immediately swapped my unit for a new one. (This one also didn’t work, so they then swapped that one for another new one). So, with minimal actual usage on the table and less than two months of ownership, I’ve already made a six hour roundtrip to Hutto and come home with a new BurnTables controller and a new Hypertherm unit, which worked perfectly prior to interfacing with their equipment and prior to their internal modification of the plasma cutter, which they assured me was a modification made based on Hypertherm’s own publication. However, according to an engineer at Hypertherm, “From Hypertherm’s perspective it is a modification that we would not authorize….as it would cause us to lose our CSA certification.”
Also worth noting from my little trip to BurnTables was that immediately upon setting up my equipment to test, their “tech support,” CJ, broke the limit switch on the Z axis of their test machine by running it down into the table. It didn’t take long before he also shattered one of their cheaply made plastic torch mounts (Below is a picture, also of their bungee cord spring for material sensing). Not very inspiring actions by the supposed expert on this table.
Now let’s talk about physics. Acceleration, force, mass, etc. The only corners that get cut well when it comes to BurnTables are the ones that save them a dime by using drastically underpowered stepper motors to power their massive gantry sluggishly around the table and decade-plus old technology for Torch Height Control. Much like any “car guy” can tell you about 1/4 mile E.T.s and 0-60 numbers, acceleration and force numbers are the parameters by which CNC cutting machines’ movements are measured. An accepted industry standard minimum acceleration rate for a table of this level is 15 inches/sec/sec. Satisfactory acceleration would fall closer to 20 i/s/s, desirable would be 35 i/s/s. Of course, these numbers are end user-adjustable in Mach 3. From the factory, BurnTables sets their tables’ acceleration at 4 inches/sec/sec. Yes, four. What this means is that it is literally impossible for their table to accelerate and decelerate at rates fast enough to maintain acceptable quality levels on any cut path that isn’t straight. This problem is compounded by the fact that a BurnTables gantry is extremely heavy (110 pounds, I weighed it), as is evident by the bent X axis shaft on their in-house vertical table, as shown in the picture below. According to CJ, this was just an “illusion” and the shaft wasn’t really bent. And according to Kyle, he’d never even noticed it before. Nice quality control work.
Also obvious on both their vertical table’s gantry as well as my standard table’s gantry was that they had designed them in such a way that one of the belts actually ran in constant contact with one of the support struts on the gantry. How this makes it even out of the design phase of their table, much less into production, is beyond me. (Quite indicative of the overall quality of their product and company as a whole, however).
The reason for the X axis shaft even exists in the first place (identical gantry on their vertical and horizontal tables) is because the entire, heavy gantry is powered by a single 400 oz/inch stepper motor (as opposed to a pair, one on each side). When I inquired with Kyle as to these extremely anemic acceleration numbers and whether or not the motors on this table could even handle 15 inches/sec/sec, I was informed, “It is your table, your can do what every you want to it. If you are wanting tech help from BurnTables, you will need to keep the table at the factory settings.”
Upon closer inspection by an engineer with 40+ years of design and manufacturing experience, it was discovered just how detrimental this combination of a single, underpowered motor, a heavy gantry, and poor acceleration and control is to cut quality, even at factory settings. Every single cut (straight lines, mind you) along the X axis of this machine exhibits a jagged edge. Cuts along the Y axis, however, are much smoother. This is clear, undeniable evidence that the above combination of factors prove to produce unacceptable results when there is movement along the X axis, even in a straight line. This means that not only are those straight lines affected, but every single curve (since a curve is combination of X and Y axis movement) suffers from reduced cut quality. The picture below is of a simple square (actually the “test” shape included with the computer from BurnTables). Notice how perpendicular sides exhibit drastically different cut quality. The Y axis only has to move the torch holder, whereas the X must move the entire gantry, which BurnTables’ factory motors and settings simply can not do. Again, this is cut at the factory settings, as packaged from BurnTables (those same factory settings that I apparently will lose access to the lifetime of tech support that supposedly comes with the table if I make changes to). To me, this is an indictment of the overall poor quality of this table and proof that it simply can not perform at an acceptable level.
13.6 miles. That’s how far I made it down the road after picking up my brand new 4x2 Burntables CNC table. I stopped to check my trailer to make sure my cargo was properly secured and was greeted by a handful of washers, nuts, bolts and bearings laying on my trailer. I promptly snapped the following picture and emailed it to Matt Kool, the salesman I dealt with at BurnTables. His reply: “Yes, a little tighter would have been preferred.”
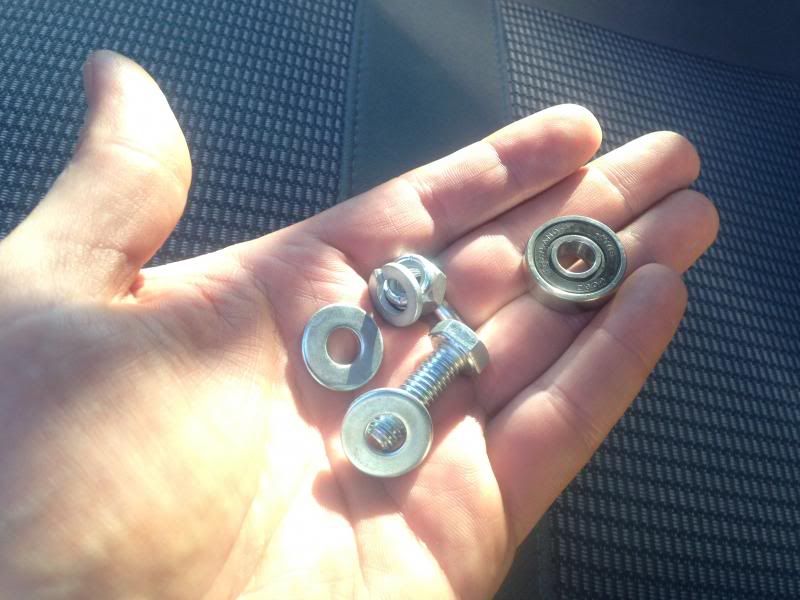
It’s also worth noting that I removed (by hand) other hand-tight bolts and bearings at this point so as not to lose them on the rest of the way home. Makes me wonder how such a table was tested at the factory prior to shipment/pick-up… This should have been my first red flag about the quality issues I was soon to experience with BurnTables, but those were actually raised before my purchase as several other victims of BurnTables’ sales pitch had advised me to stay far far away from this product. Failing to heed their advice, I did indeed end up taking the leap and making this purchase, which I have regretted literally since day one.
It took a couple of weeks before I was able to complete the installation of the table in my shop and actually begin trying to use it. Immediately, I was greeted with the following examples of the table’s work:

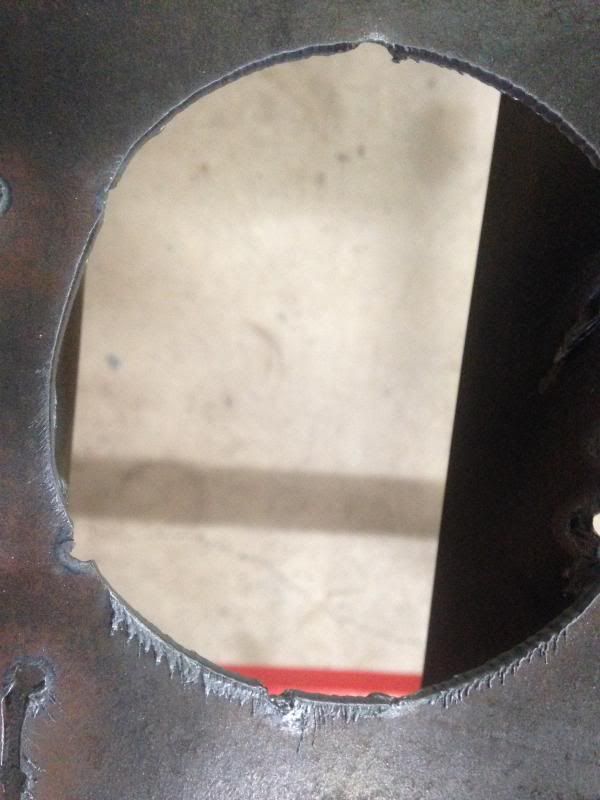
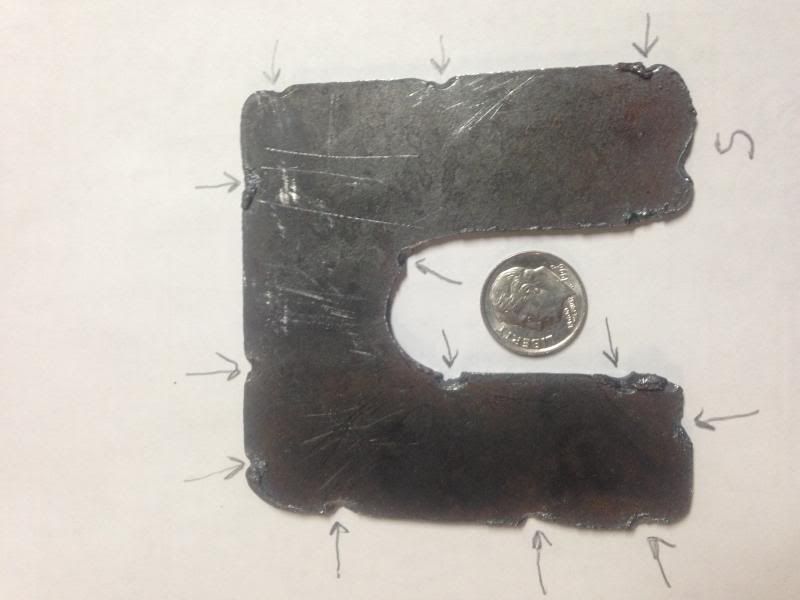
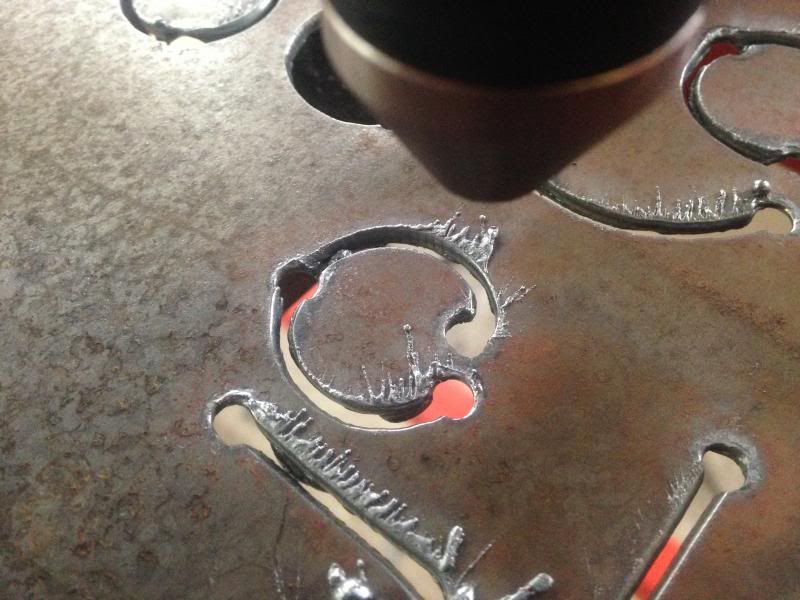
I was assured, however, that the problems I was experiencing were due to the fact that I was using a Hypertherm PowerMax 45 plasma cutter and their table’s Torch Height Control had a very small window of compatibility with this particular plasma cutter, but to keep adjusting their THC knob and eventually I would find the “sweet spot.” I finally was indeed able to eventually make what I thought were acceptable cuts. As it turns out, I would have been happy with ANY completed cut, regardless of quality. Starve a man long enough and he’ll eat anything, right? This small time frame of “success” was short lived, however, as simply changing the consumables of my machine torch threw the machine so far out of whack that I once again could not even come close to completing a cut, often not even moving the torch once the initial pierce was made. More knob turning. More knob turning. Calls to “tech support.” Instructions to keep turning the knob. Literally hours of knob turning. It was at this point I realized I was fighting an uphill battle. If this was standard operating procedure for recalibrating the machine after a simple consumables change, I was dealing with an unacceptable piece of equipment that at its best, wasn’t good enough. This is when I first asked for a refund for the table, a request which was ignored, and instead was offered the chance to send in my computer, controller, and plasma cutter for inspection and testing. Instead I packed it all up and drove it back to BurnTables myself. After a few hours onsite with Kyle Riggens (owner) and CJ Ortiz (tech support), they swapped not only my control box (because of an unknown internal issue), but also my Hypertherm unit for brand new ones. Before my experience with BurnTables, my Hypertherm was a perfectly functioning cutting unit. After they made their requisite internal modification to my torch, however, it threw an internal breaker multiple times every time I turned it on. As soon as Kyle was made aware of this, he immediately swapped my unit for a new one. (This one also didn’t work, so they then swapped that one for another new one). So, with minimal actual usage on the table and less than two months of ownership, I’ve already made a six hour roundtrip to Hutto and come home with a new BurnTables controller and a new Hypertherm unit, which worked perfectly prior to interfacing with their equipment and prior to their internal modification of the plasma cutter, which they assured me was a modification made based on Hypertherm’s own publication. However, according to an engineer at Hypertherm, “From Hypertherm’s perspective it is a modification that we would not authorize….as it would cause us to lose our CSA certification.”
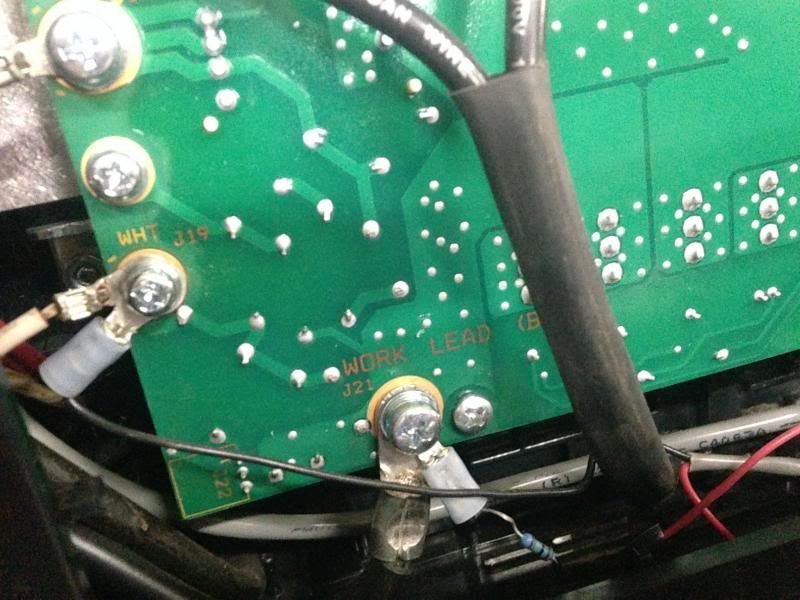
Also worth noting from my little trip to BurnTables was that immediately upon setting up my equipment to test, their “tech support,” CJ, broke the limit switch on the Z axis of their test machine by running it down into the table. It didn’t take long before he also shattered one of their cheaply made plastic torch mounts (Below is a picture, also of their bungee cord spring for material sensing). Not very inspiring actions by the supposed expert on this table.

Now let’s talk about physics. Acceleration, force, mass, etc. The only corners that get cut well when it comes to BurnTables are the ones that save them a dime by using drastically underpowered stepper motors to power their massive gantry sluggishly around the table and decade-plus old technology for Torch Height Control. Much like any “car guy” can tell you about 1/4 mile E.T.s and 0-60 numbers, acceleration and force numbers are the parameters by which CNC cutting machines’ movements are measured. An accepted industry standard minimum acceleration rate for a table of this level is 15 inches/sec/sec. Satisfactory acceleration would fall closer to 20 i/s/s, desirable would be 35 i/s/s. Of course, these numbers are end user-adjustable in Mach 3. From the factory, BurnTables sets their tables’ acceleration at 4 inches/sec/sec. Yes, four. What this means is that it is literally impossible for their table to accelerate and decelerate at rates fast enough to maintain acceptable quality levels on any cut path that isn’t straight. This problem is compounded by the fact that a BurnTables gantry is extremely heavy (110 pounds, I weighed it), as is evident by the bent X axis shaft on their in-house vertical table, as shown in the picture below. According to CJ, this was just an “illusion” and the shaft wasn’t really bent. And according to Kyle, he’d never even noticed it before. Nice quality control work.

Also obvious on both their vertical table’s gantry as well as my standard table’s gantry was that they had designed them in such a way that one of the belts actually ran in constant contact with one of the support struts on the gantry. How this makes it even out of the design phase of their table, much less into production, is beyond me. (Quite indicative of the overall quality of their product and company as a whole, however).
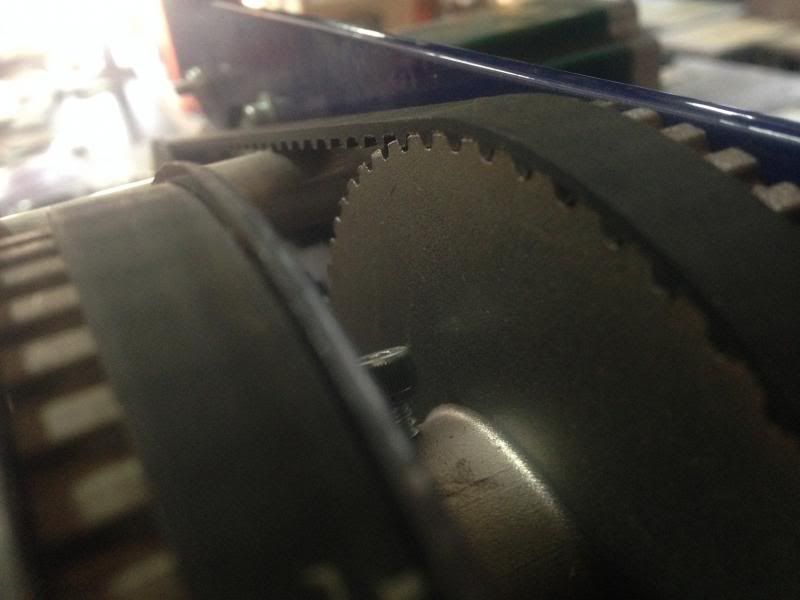
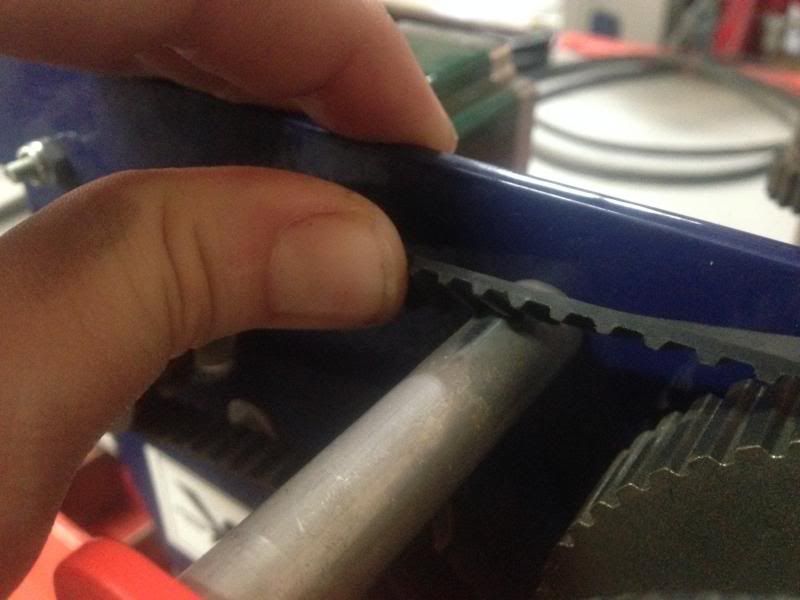
The reason for the X axis shaft even exists in the first place (identical gantry on their vertical and horizontal tables) is because the entire, heavy gantry is powered by a single 400 oz/inch stepper motor (as opposed to a pair, one on each side). When I inquired with Kyle as to these extremely anemic acceleration numbers and whether or not the motors on this table could even handle 15 inches/sec/sec, I was informed, “It is your table, your can do what every you want to it. If you are wanting tech help from BurnTables, you will need to keep the table at the factory settings.”
Upon closer inspection by an engineer with 40+ years of design and manufacturing experience, it was discovered just how detrimental this combination of a single, underpowered motor, a heavy gantry, and poor acceleration and control is to cut quality, even at factory settings. Every single cut (straight lines, mind you) along the X axis of this machine exhibits a jagged edge. Cuts along the Y axis, however, are much smoother. This is clear, undeniable evidence that the above combination of factors prove to produce unacceptable results when there is movement along the X axis, even in a straight line. This means that not only are those straight lines affected, but every single curve (since a curve is combination of X and Y axis movement) suffers from reduced cut quality. The picture below is of a simple square (actually the “test” shape included with the computer from BurnTables). Notice how perpendicular sides exhibit drastically different cut quality. The Y axis only has to move the torch holder, whereas the X must move the entire gantry, which BurnTables’ factory motors and settings simply can not do. Again, this is cut at the factory settings, as packaged from BurnTables (those same factory settings that I apparently will lose access to the lifetime of tech support that supposedly comes with the table if I make changes to). To me, this is an indictment of the overall poor quality of this table and proof that it simply can not perform at an acceptable level.
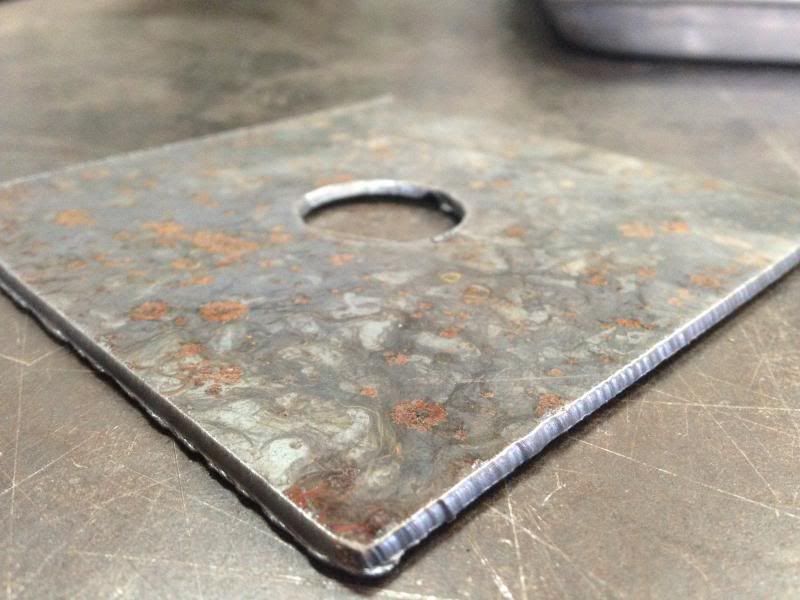