Last of the metal prep....Fuel Tanks
Finished up both tanks today. One of the tanks was in great shape on the inside and the other, well....not so much. I had picked both up off of eBay and I knew what I was getting. The not-so-hot tank was much older and had the back-in-the-day heavy baked enamel finish. The carb's fuel pick ups on this tank were filled with corroded junk but more on that later. The finished tanks are below:
To get the tank clean on the inside, I used Rustoleum liquid rust remover and steel wool on a screw driver to swish it around on the surfaces. I let the goop sit for about 20 minutes and flushed the tank with warm water. Cleaned out pretty nicely yet there was still some rust. I put a couple of handfuls of pebbles in the tank, wrapped it in an old blanket and ran it in the dryer (with no heat!) for about 30 minutes. The carbs were degreased and stripped of paint and prepped for their rebuild.
More pics of the work:
Finished up both tanks today. One of the tanks was in great shape on the inside and the other, well....not so much. I had picked both up off of eBay and I knew what I was getting. The not-so-hot tank was much older and had the back-in-the-day heavy baked enamel finish. The carb's fuel pick ups on this tank were filled with corroded junk but more on that later. The finished tanks are below:
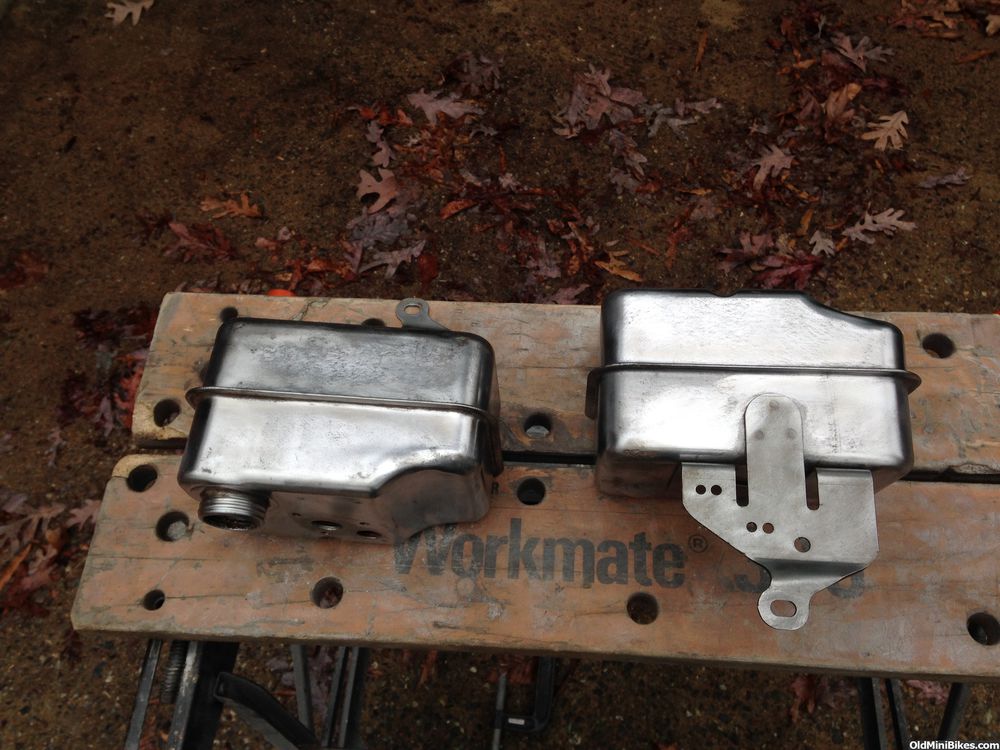
To get the tank clean on the inside, I used Rustoleum liquid rust remover and steel wool on a screw driver to swish it around on the surfaces. I let the goop sit for about 20 minutes and flushed the tank with warm water. Cleaned out pretty nicely yet there was still some rust. I put a couple of handfuls of pebbles in the tank, wrapped it in an old blanket and ran it in the dryer (with no heat!) for about 30 minutes. The carbs were degreased and stripped of paint and prepped for their rebuild.
More pics of the work:
Attachments
-
2 MB Views: 61
-
2 MB Views: 58
-
1.1 MB Views: 59
-
1.5 MB Views: 58
-
2.5 MB Views: 55
-
1.8 MB Views: 57
-
1.9 MB Views: 62
-
1.9 MB Views: 62
-
1.3 MB Views: 64
-
1.9 MB Views: 59
-
2.1 MB Views: 62